The Industrial Internet of Things (IIoT) is one of the most used set of buzzwords in recent years, but it is still poorly understood. Principle automation engineer for Beckhoff Automation, and a member of Open IIoT, Harry Mulder explains what it is and how it can help your business.
The acronym IoT and its derivative IIoT are everywhere, generating a lot of excitement whenever they arise. Yet they are still poorly understood by many. So, what do they mean and, more importantly, what can they do for your business?
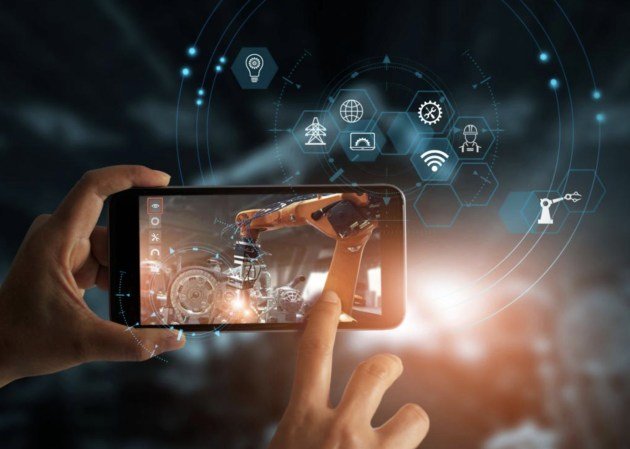
The Internet of Things (IoT) refers to the internet being used to interconnect a multitude of devices. Estimates vary, but it is believed that around 30 billion devices are currently connected to the internet – or roughly four devices for every human – and the number is growing sharply year on year.
IIoT refers to Industrial IoT, which is IoT that applies specifically to manufacturing and process industries.
IIoT again means the connecting of multiple devices to the internet, but this time all the devices are used in the industrial realm. This includes controllers (that run most industrial sites), but also a myriad of other devices, even down to individual sensors that provide simple on/off signals.
Gains from interconnectivity
There are several advantages to be gained by interconnecting devices. One problem that is overcome by large-scale inter-connectivity is that of “islands of automation”. This is where systems within a process work in isolation, but not together. The integration of automation systems with supply chains is one benefit that widespread interconnectivity can bring.
The main reason for inter-connectivity is the mass monitoring of devices. By collecting data from many devices and storing it over a long period, we can closely examine what each stage of a process is doing. We involve as many devices as we can to see the interaction between them and form a much clearer picture of operations.
” IIoT has also advanced computerised automation, with techniques such as machine learning… being used in the decision-making process.”
The stored data can be analysed, so if, for example, a product fails a quality test, we can see exactly what each component was doing throughout the manufacturing process. This helps track down the cause so that it can be rectified. Wastage is also reduced by improving the quality of output.
In the same way, we can monitor energy usage of a plant and identify causes of consumption spikes, which can be costly. Condition monitoring can also be applied to each piece of equipment, to improve its longevity and to gauge when to perform predictive maintenance. Similarly, we can improve production efficiency by detecting bottlenecks and much more.
IIoT has also advanced computerised automation, with techniques such as machine learning (ML) and other streams of artificial intelligence (AI) being used in the decision-making process. It is not practical for humans to be involved in such analysis, although they can still exert some influence over final outcomes.
Data Volumes
The volume of data even a single plant can generate is huge. It is so great that it is often referred to as “Big Data” and needs to be stored in the cloud (also known as cyberspace). Once in the cloud, high‑powered computers can trawl through the data and analyse it meticulously. Both the data storage and analytical tools needed are of such sophistication that a specialist cloud service provider is required.
While industrial sites have been able to store and monitor their production data in the past, it was always been on a much smaller scale and on site. Modern tools, such as the cloud, offer far superior facilities than previously possible.
What is Industry 4.0?
So significant is this movement towards data‑centric manufacturing, that it is being called “Industry 4.0”. This is yet another buzzword, but the four refers to the fourth major paradigm shift in manufacturing since the industrial revolution began. The first three were mechanisation in the 1800s, electrification in the 1920s and computerisation in the 1970s.
Each of these stages resulted in massive changes to the methods manufacturers employed, but also resulted in monumental increases in efficiency. This relatively new fourth stage of digitisation and data technology, also known as cyber‑physical, will be equally significant in the new efficiencies it will offer to production systems.
Increasing competition
With markets becoming more global, competition has become significantly tighter, placing still greater pressure on manufacturers to become more efficient. It is therefore vital that producers continually look for new ways to drive improvements or face the prospect of becoming uncompetitive.
IIoT, with its careful and comprehensive monitoring of an enterprise, can become part of the solution to remain competitive. Its all-encompassing nature means every aspect of a business can be analysed.
The Open IIoT Group – Six Vendors Advancing Industry 4.0
Open IIoT is a group of six vendors with the ability to collectively supply the complete range of products for industrial automation. Each one of these companies is internationally recognised as a specialist in its respective field, having gained many years of industry expertise.
Open IIoT is essentially a knowledge group that is advancing the uptake of Industry 4.0 in Australian manufacturing. The member companies are sensor and measurement specialists Balluff; Beckhoff, which produces automation controllers that link directly to the cloud; KUKA Robotic Automation and its focus on robotic solutions; leader in drive and geared motor technology NORD Drivesystems; SMC specialising in advanced pneumatic automation; and system integrator with speciality experience in IIoT systems, ZI-Argus.
As a cohort, Open IIoT aims to assist industrial customers in getting started on their Industry 4.0 implementation and, more importantly, show them the commercial benefit that this implementation can deliver.
They can show how IIoT, being an open rather than propriety technology, can integrate with existing systems that a site may already use. Open IIoT works hard to understand customers’ needs and make a point of cutting through the jargon to help them achieve their goals of enhancing their competitiveness.
About the author

Harry Mulder is the principle automation engineer for Beckhoff Automation.
Source: This article first appeared in the July 2021 issue of Food and Drink Business.