In this PKN exclusive round-table discussion with Open IIoT, Australia’s leading cohort of Industry 4.0 and automation experts, we find out from where things are at… after Covid.
It’s ironic that the COVID-19 pandemic, a health crisis that wreaked havoc around the globe, can be considered as having a positive impact by being the catalyst for widespread Industry 4.0 adoption in Australia.
In the face of lockdowns and work-from-home orders, a number of manufacturers realised that implementing Industry 4.0 technologies into their factory floor allowed them to have remote access to their machinery data and to be able to operate production remotely: including making changes and doing maintenance.
With remote access to data, manufacturers could now predict outputs, make changes as required in their production and pivot as needed – all at the touch of a button, even when they couldn’t physically be on the factory floor. All of a sudden, Industry 4.0 knowledge and technologies became very valuable to many companies, with Statista reporting that over 40 per cent of Australian manufacturers intend to invest in the emerging technology area relating to intelligent automation and robotic process automation over the next two to three years.
The Open IIoT Group, an initiative of some of Australia’s most prominent automation brands, founded with the mission of making these complex concepts more accessible, has observed a remarkable uptick in Industry 4.0 adoption in the last three years.
They share their insights on the State of the Industry below.
What has been the feedback from Australian customers who have adopted Industry 4.0 technologies?
“The ANZ market has been one of the most innovative markets for our company with local customers across a range of industries embracing smart solutions such as sensorless oil change monitoring, real-time energy consumption feedback, and smart Programmable Logic Controllers (PLCs).
“The feedback that we get from our customers is that smart plug-and-play solutions enable them to install projects faster and with less manpower. Due to modern ethernet-based connectivity, Australian customers can program and service their machines remotely, which is a huge advantage.”
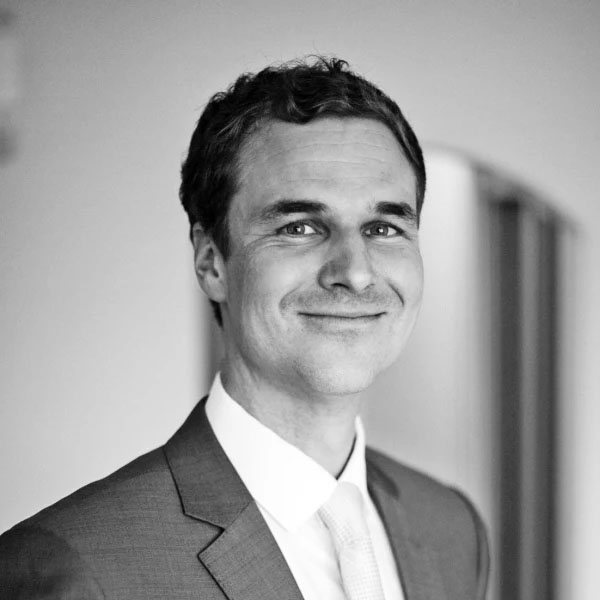
Max Jarmatz
Managing director at Nord Drivesystems
What are the roadblocks to implementation and how can we leapfrog them?
“Often, the roadblocks arise from local manufacturers inability to connect tangible commercial value to the initial investment. It’s important to keep in mind that the cost of implementation relates directly to the digital maturity of the systems already in place. It has been found on average that in 60 per cent of the cases, the existing equipment on site is already equipped with extended functionality that has not been utilised. Investing the time in understanding the full functional capabilities of the existing equipment in place, combined with having clearly defined outcomes for implementation can help to unlock the desired commercial value.”
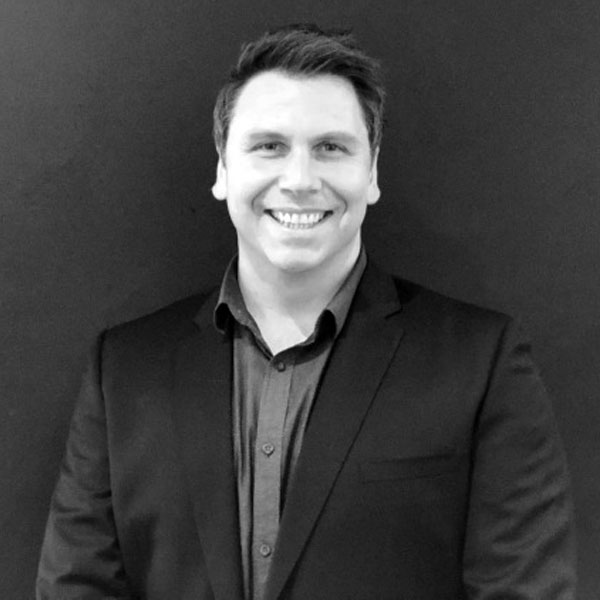
Jozef Ceh
SMC Corporation Digital Transformation and Industry 4.0 manager
What new technologies do you think have the possibility to create smart factories?
“Creating a ‘smart’ factory is about having real-time visibility, being flexible and learning to react to internal and external changes in the manufacturing process. Artificial Intelligence (AI) has the potential to make this a reality and learn from multiple inputs. For Balluff this is a really exciting development – as a sensor supplier, we enable a large portion of the condition monitoring and information generation required to feed into these AI systems. These will enable previously unseen insights and predictions and drive fast changes in production to improve quality and efficiency.”

Jim Wallace
National sales manager at Balluff Australia
Where do you see the Australian manufacturing industry 10 years from now? What do you think is needed to get there?
“The pandemic exposed Australia’s overreliance on imported materials following disruptions to the supply chain. This brought about a renewed call to reshore manufacturing and produce more locally.
“In the past, the majority of goods were sourced from overseas due to Australia’s higher labour costs making local production less cost-effective. But recent surveys have revealed that consumers are now willing to pay slightly more in return for locally-manufactured goods. While higher labour rates remain a significant barrier for local producers, its impact can be mitigated through the use of innovative tools such as automation and robotics as modern technologies are key to the successful transformation of the industry.
“We believe manufacturing in Australia has a bright future, particularly in areas where we have natural advantages, such as food processing for our agriculture sector and metallurgy for mining industries. Government assistance and increased Industry 4.0 adoption will help us to secure our position as global leaders in manufacturing in the next decade.”
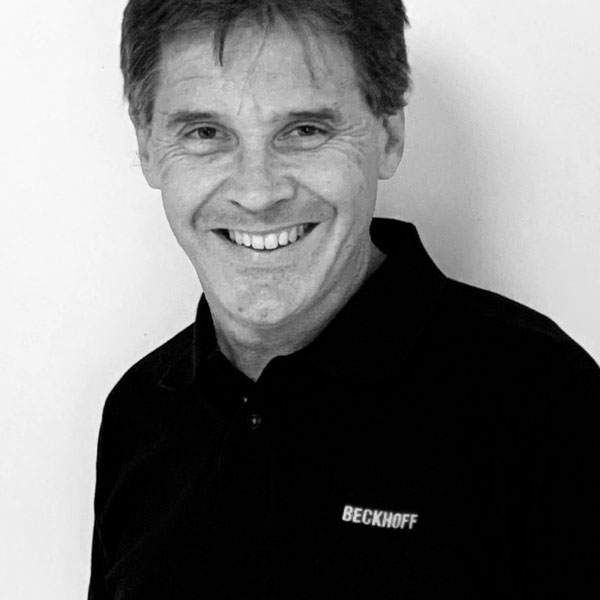
Harry Mulder
Principal automation engineer at Beckhoff Automation
This article was first published in the PKN January-February 2023 print issue. Check it out Here