The confectionery industry is one of the fastest growing sectors. Many new packaging ideas are implemented using innovative technical concepts. LoeschPack, a leading manufacturer of packaging machines with headquarters in Altendorf, Germany, is one of the first companies to use the advantages of the new IO-Link communication standard. There it is used on a stacking unit which is part of the new LRM-DUO packaging machine. “The result is impressive. Expensive bus cables are no longer needed, there is no more cumbersome parallel wiring and the system has become significantly more compact,” notes Deputy Manager of Electrical Design Ulrich Hausner.
The modular, twin station high-performance fold wrapping machine for chewing gum and chocolate multipacks runs at a cycle rate of 200 pcs./minute to box and then tightly wrap with cellophane small rectangular candies such as chocolate bars and chewing gum sticks. An IO-Link equipped, modular, automatic stacker ensures reliable and efficient delivery of the cardboard packaging.
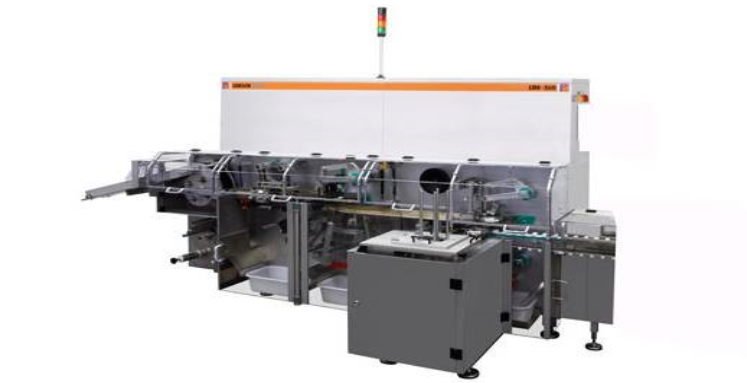
A particular challenge is presented by the variety of movements within the system which interact with each other at high speed and therefore have to run with strict coordination and absolute reliability. LoeschPack relies on the combination of mechanical, cam-controlled drives using a central drive shaft together with servo-driven movements. The vertical shaft has hardened, machine-specific configured cam discs with specially calculated curve profiles which ensure that all movements and units are always coupled, so that everything is coordinated with the main drive even at high speeds. The decision to use servomotor or mechanical drive is always made depending on the application and its requirements. “With numerous single motors as the drive you wouldn’t have the desired extremely high reliability over the long haul,” notes Ulrich Hausner. The goal is always to implement the most logical combination of mechatronic systems. Evaluation criteria such as safety, operability and technical reliability are always in the foreground.
IO-Link as communication standard
With IO-Link LoeschPack is not using a new kind of bus system on the new machine, but rather an unusually versatile communications standard comparable with the USB interface in the computer world. Both are cost-effective, po8int-to-point connections for signal and power transmission which can be operated in a plug and play manner. Whereas USB has long been a standard for fast and inexpensive connection of computer peripherals, IO-Link is poised to play a comparable role as an installation system for connecting sensors, actuators, operating and display elements in machine building.
One special feature: the new communications standard is downward compatible with all standard sensors and immune to noise. For the user this means he can, but is not required, to use sensors and actuators having the IO-Link interface in order to enjoy benefits.
In technical terms, data transmission using IO-Link is always between an IO-Link master and a connected IO-Link device as slave. IO-Link masters can be field bus modules, typically rated IP 67, or PLC interface modules. Binary sensor signals are collected using special sensor hubs.
The serial IO-Link interface requires only a common, 3-conductor standard cable. Costly bus cables, shielded or unshielded special cables are not needed, nor are additional connection boxes. This radically simplifies the entire installation process, since the cabling now just take a fraction of the time it used to – not to mention the cost savings.
Installation details
Specifically the IO-Link installation at LoeschPack looks like this: electronic control of the machine is handled by a Simatic S7 PLC together with a SIMATIC ET 200S peripheral with Profibus interface, both from Siemens.
Used as masters in the control cabinet of the stacker module are two ET200S 4S1 interface cards rated to IP 20, each with four IO-Link ports. Connected to these are 7 Balluff IO-Link 8xM8 sensor hubs rated to IP67. At the stacker unit they gather the signals from the switching photoelectric sensors which monitor the minimum height of the carton stack. Eight inputs each are bundled through a sensor hub to an IO-Link port, so that they can be made available to the machine controller using simple, unshielded standard cable via IO-Link to the master and from there via Profibus to the controller. Passive Balluff splitter boxes are also used to send safety-relevant signals from additional photoelectric signals “No cardboard left – then E-STOP” directly to a Pilz safety module.
The special advantages of the IO-Link installation: LoeschPack saves the cumbersome wiring for the 42 photoelectric sensors, since the sensor hubs concentrate 8 or 16 inputs depending on the version into one IO-Link port. “This not only reduces the installation time involved compared with previous solutions, it also eliminates expensive bus cables, and without the thick cable harnesses we have been able to make the stacker unit much more compact.”
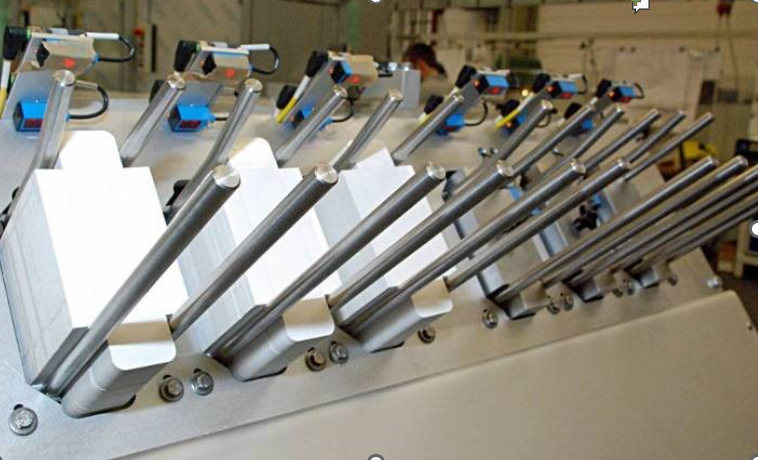
For existing systems, this new installation concept gives LoeschPack the option of simply and compactly expanding systems or even carrying out complete retrofit work by plugging in IO-Link interface cards. The existing IOs can still be used while decentralized installation using IP67 devices is
possible. Extremely high channel density can be accomplished in the smallest space with just one IO-Link master and 4 sensor hubs each with 16DI taking up just 15mm of installation width.
The 3-conductor cable needed for the IO-Link installation shortens is shortened by the machine builder himself from two standard output sizes to the desired length so that it can be assembled to Balluff connectors. This means “no loops or pigtails from excess cable lengths which take up additional space in the machine or cable ducts,” explains Ulrich Hausner.
Smooth interplay
“We very consciously chose the Balluff IP67 sensor hubs,” continues Hausner. “The attractive design, the high functionality, the compact size and ease of handling got our attention from the outset.” With a cycle time of just 2.5 ms the hubs (version without diagnostics function) are a perfect match for the Siemens master with its cycle time of 5 ms. Linking the IP67 world to the ET200S peripheral with IP20 protection thus became child’s play. “Here it’s also clear,” notes Hausner, “that the interplay between various IO-Link devices, even if they come from different manufacturers, works like a charm. The IO-Link standard in its current iteration ensures high interoperability.”
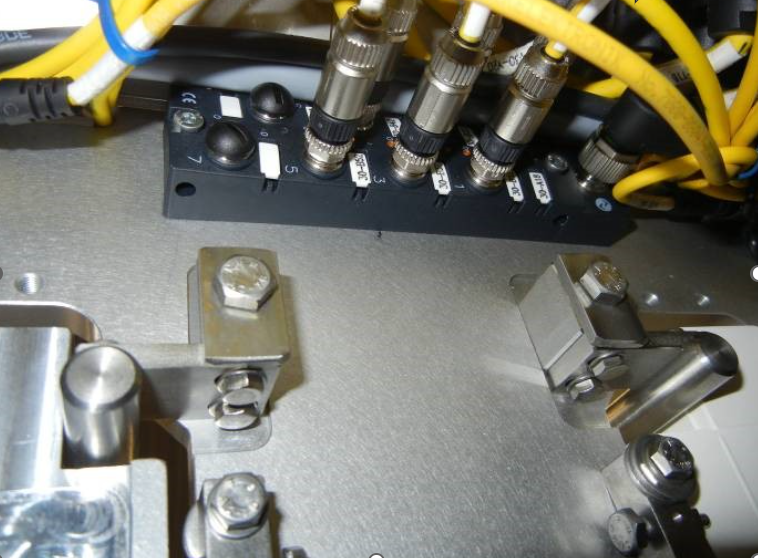
Of current interest to LoeschPack is the use of IO-Link especially with mobile modules such as end stackers, conveyor belts, etc. These need to be designed as compact and space-saving as possible.
In this specific case Hausner sees no advantages to full implementation of IO-Link throughout the entire packaging machine. The control cabinet – typical of many machines offered by LoeschPack – is located above the dirtyh area directly on top of the machine. This means the cable lengths are extremely short. The threaded fittings and seals on the control cabinet are sufficient for the use of cleaning processes. Changing from the IP20 world to the IP67 protection offered by IO-Link would bring no advantages.
Looking ahead
IO-Link could however prove useful one day for different reasons. Stefan Horcher, sales engineer at Balluff, sees here much untapped potential: “The new communications standard represents not only time-saving, lean cab ling, but also simplified parameterization and diagnostics concepts.” This makes sense especially when large numbers of configurable IO-Link sensors and actuators are installed in the system. These can have their parameters set centrally and software-based using data-and function modules, regardless of where the devices in question are physically located. In Horcher’s experience some machine builders use these features to parameterize the entire system in one go after the machine comes off
the line. This not only shortens startup time, but also the entire time-to-market phase, which is a key selling feature. This possibility also benefits the user by drastically reducing the time to switch to a new ‘recipe’.
Diagnostics is another area opened up by IO-Link. Since machines from LoeschPack are in use all over the world, reliable remote maintenance concepts have high priority. Here IO-Link sensors and actuators have a distinct advantage, since they provide a clear view of the process level. When there is a fault the service technician can see in detail what is wrong with the sensor or actuator. Perhaps just one sensor has gotten dirty and set the corresponding message bit. In any case the machine operator is provided with clear diagnostics and specific tips for remedying the problem.
Loesch Verpackungstechnik GmbH – or simply “LoeschPack” for short – is an international leading manufacturer of packaging machines and complete packaging systems for chewing gum, chocolate, dry baked goods. Founded in 1919 and with headquarters in Altendorf, Germany, the company is today part of the Piepenbrock Group with over 25,000 employees and exports accounting for 90% of sales. It acts as a reliable partner and systems provider for the confectionery industry to provide comprehensive service around the globe. If desired LoeschPack can team with its customers over the entire service life of their machines, from the concept to engineering, building and startup, followed by training and spare parts provision.
Balluff GmbH offers a full range of high-quality sensors, linear transducers and identification systems as well as networking and connectivity solutions for every area of factory automation. Founded in 1921 and family owned and run for four generations, Balluff invests a high percentage of revenue in research and development. Production and engineering facilities as well as subsidiaries and representatives are distributed around the world. Manufacturing is carried out not only at the headquarters in Neuhausen a.d. Fildern/Germany, but also at six additional facilities in Hungary, Switzerland, the USA, Brazil, Japan and China.